In today’s fast-paced manufacturing industry, maintaining optimal efficiency and productivity is crucial for success. To achieve this, businesses turn to advanced technological solutions, one of which is the shop floor control system. But what exactly does this system entail, and why is it so vital in modern manufacturing processes?

A. Definition of Shop Floor Control System
The Shop Floor Control System is a comprehensive software solution designed to streamline and optimize various aspects of the manufacturing floor. It acts as a centralized hub that enables real-time monitoring, reporting, and management of operations, resources, and processes. From work order management to production scheduling, this system provides a holistic approach to enhance overall efficiency and control.
B. Importance of Shop Floor Control System in Manufacturing
In the highly competitive manufacturing landscape, staying ahead of the curve is essential. A Shop Floor Control System offers numerous benefits that directly address the challenges faced by manufacturers. By leveraging this system, businesses can effectively monitor and manage their production floor, leading to improved productivity, reduced costs, enhanced quality control, and increased customer satisfaction.
Efficient production scheduling and planning ensure that resources are allocated optimally, reducing downtime and maximizing output. Real-time monitoring and reporting capabilities provide valuable insights into the status of machines, labor, and work orders, enabling quick decision-making and proactive problem-solving. Additionally, the system facilitates effective inventory management, ensuring the availability of materials and minimizing waste.
When manufacturers implement a Shop Floor Control System, they can achieve higher levels of operational efficiency, quality control, and resource utilization. With such control and insight at their fingertips, businesses can streamline their processes, respond swiftly to changing demands, and maintain a competitive edge in the market.
So, how can you harness the power of a Shop Floor Control System to revolutionize your manufacturing operations? Let’s delve deeper into its key features and explore the benefits it can provide in the next sections. Stay tuned for an enlightening journey into the world of shop floor control systems!
Key Features of a Shop Floor Control System
To fully grasp the significance of a Shop Floor Control System, it’s essential to understand its key features and how they contribute to optimizing manufacturing processes. Let’s dive into the functionalities that make this system an indispensable tool for manufacturers:
A. Real-time Monitoring and Reporting
With real-time monitoring capabilities, a Shop Floor Control System provides up-to-date visibility into the manufacturing floor. It allows you to track the progress of production, monitor machine performance, and identify any bottlenecks or issues that may arise. By collecting real-time data, you can make informed decisions promptly, ensuring smooth operations and efficient resource allocation.
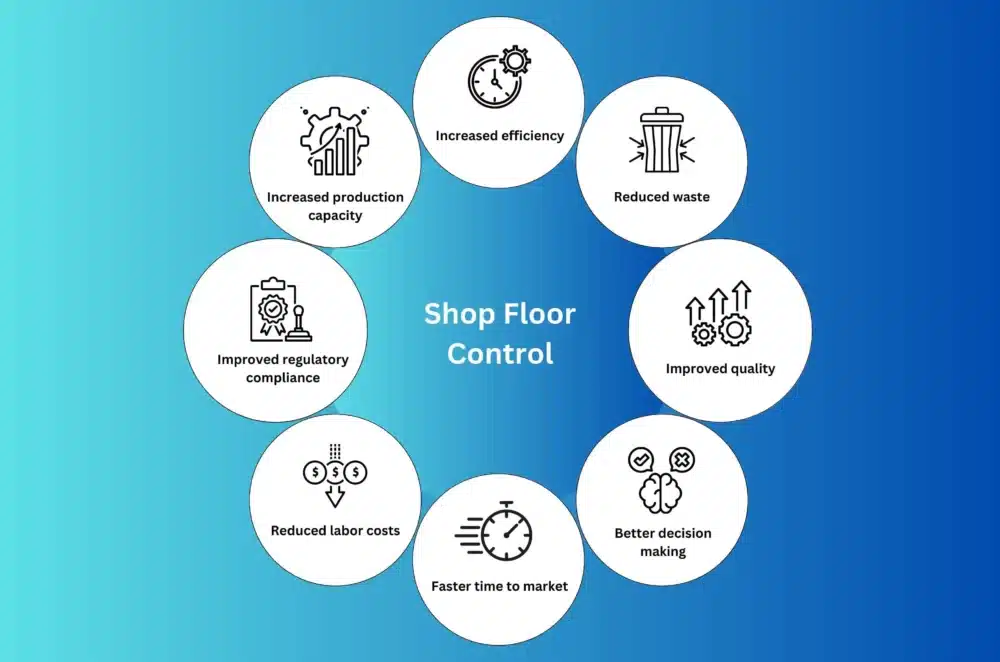
B. Work Order Management
Efficient work order management is crucial for maintaining order and organization in manufacturing operations. A Shop Floor Control System enables you to create, assign, and track work orders seamlessly. It provides a centralized platform where you can allocate resources, set priorities, and monitor the status of each work order. This feature ensures that tasks are completed on time, reducing delays and improving overall productivity.
C. Machine and Labor Tracking
Tracking machines and labor is vital for optimizing resource utilization and productivity. The Shop Floor Control System allows you to monitor machine performance, downtime, and maintenance schedules. It also enables you to track employee activities, such as time spent on specific tasks and attendance. By having clear visibility into these aspects, you can identify areas for improvement, optimize workflow, and ensure optimal utilization of resources.
D. Quality Control and Inspection
Maintaining high product quality is a top priority for manufacturers. With a Shop Floor Control System, you can implement robust quality control and inspection processes. The system enables you to define quality standards, conduct inspections, and record any defects or deviations. By proactively addressing quality issues, you can minimize rework, reduce waste, and ensure that only products meeting the highest standards reach the market.
E. Inventory Management
Efficient inventory management is critical to avoid stockouts, reduce carrying costs, and streamline production. A Shop Floor Control System offers comprehensive inventory management capabilities, allowing you to track inventory levels, monitor material usage, and automate replenishment processes. By optimizing inventory levels and ensuring timely availability of materials, you can minimize production disruptions and improve overall efficiency.
F. Production Scheduling and Planning
Effective production scheduling and planning are key to meeting customer demands and maximizing resource utilization. The Shop Floor Control System provides tools to create dynamic production schedules, considering factors such as machine availability, labor capacity, and material availability. By optimizing production plans, you can minimize downtime, reduce lead times, and ensure on-time delivery of products.
In the next section, we will explore the benefits that implementing a Shop Floor Control System can bring to your manufacturing operations. Stay tuned to discover how this system can revolutionize your business!
Benefits of Implementing a Shop Floor Control System
Incorporating a Shop Floor Control System into your manufacturing operations can yield a multitude of benefits. Let’s explore how this powerful solution can drive efficiency, improve quality control, enhance visibility, streamline communication, and optimize inventory management.

A. Increased Efficiency and Productivity
With a Shop Floor Control System, you can optimize your manufacturing processes by eliminating bottlenecks and reducing downtime. Real-time monitoring and reporting capabilities enable you to identify and address issues promptly, ensuring smooth operations and minimizing production delays. By streamlining workflows and automating manual tasks, the system empowers your workforce to focus on value-added activities, resulting in increased productivity and output.
B. Improved Quality Control and Reduced Errors
Maintaining high-quality standards is paramount in manufacturing. A Shop Floor Control System enables you to implement robust quality control measures throughout the production cycle. The system facilitates real-time inspections and data collection, allowing you to detect and rectify potential errors before they escalate. By enforcing standardized procedures and providing visibility into quality metrics, you can ensure consistent product quality, reduce rework, and mitigate the risk of defects or recalls.
C. Enhanced Visibility and Transparency
Gaining real-time visibility into your manufacturing operations is vital for effective decision-making and resource allocation. A Shop Floor Control System offers comprehensive insights into machine performance, labor utilization, and work order statuses. This transparency allows you to identify inefficiencies, identify trends, and make data-driven decisions to optimize operations. With a clear view of your entire production floor, you can respond swiftly to changing demands, proactively manage resources, and drive continuous improvement.
D. Streamlined Communication and Collaboration
Effective communication and collaboration between different departments and teams are critical for seamless operations. A Shop Floor Control System acts as a centralized platform for sharing information, streamlining communication, and fostering collaboration. By providing real-time updates and notifications, the system ensures that everyone is on the same page, enabling efficient coordination and problem-solving. This collaborative environment promotes cross-functional teamwork and empowers employees to work together towards common goals.
E. Optimized Inventory Management and Cost Control
Inventory management plays a crucial role in cost control and meeting customer demands. A Shop Floor Control System offers robust inventory management features, enabling you to track materials, monitor stock levels, and optimize replenishment. By minimizing stockouts, reducing excess inventory, and optimizing material usage, you can effectively control costs and improve cash flow. With accurate inventory data at your disposal, you can make informed purchasing decisions, avoid wastage, and ensure timely delivery to customers.
By implementing a Shop Floor Control System, you can unlock these remarkable benefits and revolutionize your manufacturing operations. Next, let’s explore the key factors you should consider when choosing the right system for your business.
Factors to Consider When Choosing a Shop Floor Control System
When selecting a Shop Floor Control System for your manufacturing operations, several crucial factors need to be taken into account. The right system can significantly impact your productivity, efficiency, and overall success. Let’s explore the key considerations to ensure you make an informed decision.

A. Scalability and Customizability
As your business grows, so will your manufacturing needs. It’s vital to choose a Shop Floor Control System that offers scalability, allowing it to adapt and accommodate increasing demands. A scalable system ensures that you can expand your operations without encountering limitations or the need for a complete overhaul. Additionally, customizability is essential to tailor the system to your specific requirements and workflows.
B. Integration with Existing Systems
To avoid disruptions and ensure a smooth transition, it’s crucial to select a Shop Floor Control System that seamlessly integrates with your existing systems. Compatibility with your enterprise resource planning (ERP) software, manufacturing execution system (MES), and other essential tools is vital for data synchronization and efficient operations. Integration minimizes manual data entry, reduces errors, and facilitates a holistic view of your manufacturing processes.
C. User-Friendliness and Ease of Implementation
Implementing a new system can be a complex task, often involving training and adjustments. Opt for a Shop Floor Control System that offers a user-friendly interface and intuitive features. A system that is easy to navigate and understand streamlines the implementation process and reduces the learning curve for your team. Look for a solution that provides comprehensive documentation, training resources, and responsive customer support.
D. Vendor Support and Maintenance
When investing in a Shop Floor Control System, reliable vendor support and maintenance are essential. Choose a vendor with a proven track record of providing timely assistance, software updates, and bug fixes. Regular maintenance ensures that your system remains up to date, secure, and optimized for performance. Additionally, consider the vendor’s reputation and customer reviews to gauge their reliability and commitment to customer satisfaction.
E. Cost and Return on Investment
Budget considerations play a significant role in selecting a Shop Floor Control System. While it’s essential to find a system that aligns with your financial capabilities, don’t compromise on functionality and quality. Assess the long-term return on investment (ROI) by evaluating the system’s potential to improve productivity, reduce costs, and enhance efficiency. Consider factors such as licensing fees, implementation costs, ongoing maintenance expenses, and potential savings or revenue generation.
By carefully considering these factors, you can confidently choose a Shop Floor Control System that meets your manufacturing needs and sets your business on a path to success. In the next section, we will explore the best practices for implementing a Shop Floor Control System, ensuring a seamless integration into your operations.
Conclusion
In conclusion, implementing a Shop Floor Control System can revolutionize your manufacturing operations, providing you with the tools and insights needed to optimize efficiency, productivity, and quality control. By streamlining processes, monitoring resources in real-time, and enhancing communication and collaboration, this system empowers businesses to stay ahead of the competition in the ever-evolving manufacturing landscape.
To successfully implement a Shop Floor Control System, it is crucial to follow best practices that ensure a seamless transition and maximize the system’s benefits. Begin by assessing your current processes and identifying specific needs and pain points. This evaluation will help you determine the features and functionalities required from a system and identify areas for improvement.

Next, carefully select the right system and vendor that aligns with your business goals and requirements. Consider factors such as scalability, customizability, integration capabilities, user-friendliness, and ongoing support.
Once you have chosen a system, create a comprehensive plan for implementation, taking into account factors such as timeline, resource allocation, and change management strategies. Ensure that all stakeholders are involved and communicate effectively throughout the process.
Training and onboarding employees are critical to the successful adoption of the Shop Floor Control System. Provide comprehensive training sessions and resources to familiarize your team with the system’s functionalities and benefits. Encourage their active participation and address any concerns or questions they may have.
Lastly, continuous monitoring and improvement are essential to ensure the long-term success of the system. Regularly analyze data, gather feedback, and make necessary adjustments to optimize processes and maximize the system’s potential.
By following these best practices, you can unlock the full potential of a Shop Floor Control System and pave the way for a more efficient, productive, and successful manufacturing operation. Embrace the power of this transformative technology and take your business to new heights.